Picture this: A refinery operating smoothly, everything seemingly under control. Then, a steam leak goes unnoticed. Ice builds up, and eventually, a chunk the size of a mini fridge falls down.
Fortunately, no one is injured. But the incident raises questions: “How did this happen? Why wasn’t it caught sooner? How can we prevent it next time?”
Next comes the solution: a Digital Preventive Maintenance Program.
Using advanced drone technology to capture the entire facility, photogrammetry, NDT and thermal data is then converted into exact 3D models. Logging in online, specialists can then conduct virtual identification, analysis and preventive reporting to target and avoid potential risks ahead of time.
This is the real-life incident shared by Courtland Penk, President of Osprey Integrity, in our recent webinar.
It’s a powerful example of how preventive maintenance strategies can not only reduce OT and exposure hours in high-risk environments, but also ensure that even the smallest hairline crack isn't missed.
Reactive vs. Preventive maintenance
For decades, maintenance teams have traditionally relied on manual observations, written reports, and historical engineering drawings, to understand on the condition assets.
However, these methods can be time-consuming and extend site shutdown periods, due to a reliance on abseiling/rope access, cranes, and heavy machinery. Additionally, these manual observations may miss critical defects in hard-to-reach or hazardous zones, such as the top of a flare.
Today, 3D software solutions like Trendspek are supporting the evolving O&G industry through safer, scalable, and repeatable asset management and monitoring.
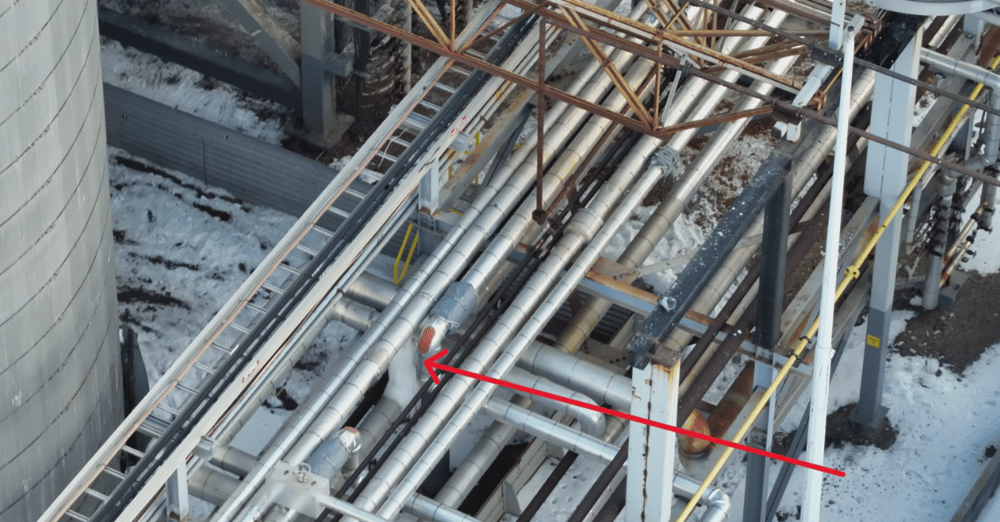
Teams can also zoom in on a specific valve, or zoom out to assess an entire row of tanks. With millimetre detail on-screen, they can spot potential risks before they escalate into costly failures.
Courtland Penk, President at Osprey Integrity says:
“To just drop a pin in a 2D map only tells half the story. To make corrective actions, we need to know what it’s like vertically as well. That’s where 3D solutions maximise value. It's not just about data and showing positional information, it's also about trying to alleviate some of the paperwork in the long run."
Key takeaways from the webinar
Technology Enables Cultural Change
“Technology is certainly the enabler to the people, process, and culture changes that have to happen within the business. There’s real value along the way that will just lead to more value with fewer headaches. Early adopters of these technologies are setting themselves up for massive advantages in the next few years.”
Efficiency Through Data Consolidation
“It's not just about data and showing positional information, but it's about trying to alleviate some of the paperwork in the long run. The efficiency and availability of the data then leads to the actionable insight, rather than death by folders.”
“The more that we can consolidate and improve the access and delivery, the viewability, the interaction with that data, the more you're empowering those subject matter experts to provide actionable insights at your facility.
Getting Ahead with Maintenance Needs
"The tools and the way that we can view and provide that kind of information, and also summarize risks and repair process, all in the same environment, you start to tick some boxes."
📈 The measurable benefits
Virtual walkthroughs to anticipate access, resources, risk severity
With 24/7 access to 3D models, teams can conduct virtual site walkthroughs to anticipate resources required90% structural coverage
Millimetre detail of asset exteriors, including insulation, leaks, ventilation, thermal, and structural hardware.Interactive repair packages
Shareable 3D models with accurate specs allows for an improved system of engagement.